تکنولوژی جدید iMFLUX
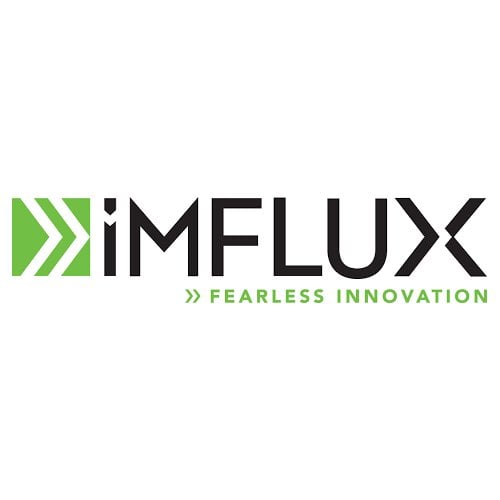
iMFLUX ، یک فرآیند قالب گیری تزریق جدید است که با استفاده از فشار کم و ثابت برای دستیابی به چرخه های سریعتر و قطعات با کیفیت بهتر، تمام قوانین را تغییر می دهد.
شرکت Procter & Gamble به طور گسترده ای به عنوان تولید کننده محصولات مصرفی شناخته شده است، اما شاید کمتر کسی از فعالیت گسترده این شرکت در خاطر تحقیق و توسعه در زمینه بهبود تکنولوژی پردازش پلاستیک باخبر باشد. چند سال پیش، P & G به این نتیجه رسید که نیاز به کاهش هزینه ها و زمان اجرای طرح های جدید پلاستیکی دارد.
هدف این بود که به طور کامل پروسه ی تزریق قطعات مصرفی را بازنگری کنند که به پیشرفت در سرعت، هزینه و کیفیت ساخته شده است. تحقیقات گسترده ای در این زمینه توسط متخصصان تکنولوژی قالب گیری تزریق این شرکت انجام شد. پس از تحقیقات جامع، تست و استفاده در مقیاس آزمایشی، این تیم موفق به توسعه تکنولوژیکی جدیدی با استفاده از فشار پایین و ثابت تزریق گردید. این فرایند جدید، تفکر متفاوت در مورد چگونگی طراحی قطعات و قالب ها را امکان پذیر می کند. با این کشف جدید، شرکت P&G تصمیم گرفت که iMFLUX Inc. را به عنوان یک شرکت مستقل ولی تحت مالکیت خود، راه اندازی کند. شرکت iMFLUX که در سال ۲۰۱۳ تاسیس شده است، این فناوری را به صورت انحصاری ارائه می دهد. همچنین خدمات انحصاری این تکنولوژی هم منحصرا در شرکت iMFLUX Inc.، واقع در همیلتون، اوهایو تامین می شود.
قالب گیری معمولی یا فرایند 2 مرحله ای مدتی است که در صنعت مطرح بوده است. هر چند وقت یکبار، تکنولوژی جدیدی پیش میآید تا اوضاع را کمی تکان دهد. iMFLUX یکی از این موارد است.
فرایند تزریق جدید iMFLUX شامل یک کنترلر تخصصی است که امکان پر کردن قالب را با یک میزان فشار ذوب پایین تر تعریف می کند و اجازه می دهد سرعت پر شدن به صورت خودکار با هندسه قطعه تولیدی هماهنگ گردد. از مزایای این تکنولوژی می توان به بهبود کیفیت قطعه تولیدی، امکان ایجاد طراحی های جدید قالب، بهبود پایدار و کاهش هزینه های سرمایه گذاری اشاره کرد.
بزرگترین موفقیت این نوآوری، که غیرمنتظره و غیرمعمول بود، کشف این نکته بود که پر کردن قالب به آرامی، باعث افزایش سرعت سیکل تولید می شود.
این روند در عین حال دارای معایبی نیز می شد ، به عنوان مثال این فرایند به طور کلی باعث فشار بسیار بالا به قالب می شود. از آنجا که در این روش سرعت پر شدن قالب به صورت کنترل شده می باشد، فشاری که مواد مذاب به قسمت های مختلف قالب وارد می کند، بسیار متغیر می باشد.
این شکل نشان می دهد که چگونه فشار در طول تزریق نمونه های معمولی، به شکل متعارف تغییر می کند. این فشارهای متغیر ذاتی در یک روش تزریق متعارف منجر به مشکلات متعددی از جمله جمع شدگی (یا پیچش)، تغییرات ابعاد، سوختگی و عدم پر شدن جداره قطعه می شود.
فرایند iMFLUX این مسائل را با استفاده از یک فشار پایدار کم در پر شدن قالب حل می کند که منجر به فشار یکنواخت در بخش های مختلف قالب می شود. این بدان معناست که به جای استفاده از یک سرعت ثابت تزریق، جهت ثابت نگه داشتن فشار، سرعت مجاز است که تغییر کند.
این شکل نشان می دهد که سرعت در طول فرآیند iMFLUX متفاوت است.
**
پرکردن تدریجی منجر به سرعت سیکل بالاتر می گردد:
تکنولوژی iMFLUX روند قالب گیری را با فشار پلاستیک کنترل می کند، این برخلاف روش معمول برای پر کردن قالب با توجه به میزان سیالیت و با تکیه بر سرعت روندگی مواد می باشد. کنترل فرآیند توسط فشار ذوب پلاستیک باعث می شود که مواد ذوب شده بدون گیرکردن و به آرامی وارد حفره های قالب گشته و قالب را پر کند. فشار ثابت و غیر نوسانی به طور مداوم سبب پیشروی جریان در هر نقطه می گردد، حتی در جاهایی که قطعه دارای دندانه و یا حفره و یا شکل هندسی خاصی باشد.
این روند بر اساس خنک شدن پلاستیک مذاب در قالب و ایجاد مقاومت در برابر جریان است که با ثابت بودن فشار پشت مواد، مسیر جریان با ثبات و به آهستگی پر شده و نیز قطعه تولیدی از تراکم خوبی برخوردار خواهد بود.
عکس های نزدیک از یک فرآیند iMFLUX و یک فرآیند تزریق معمولی را نشان می دهد. همانطور که می بینید، تراکم مواد در طول مسیر جریان در iMFLUX به صورت یکنواخت می باشد.
**
در فرآیند iMFLUX سرعت پرشدن قالب کندتر میشود، اما در نهایت کل چرخه سریعتر صورت می پذیرد. برای این اتفاق چندین عامل کمک کننده وجود دارد:
- نرخ پایین پر شدن باعث افزایش یکنواختی قطعه می شود که پس از آن زمان خنک سازی کمتری نیاز است.
- قالب به گونه ای آهسته پر می شود که قالب “به صورت پر شده” بسته می گردد، بنابراین ماده به طور مداوم در تماس با دیواره های قالب، همزمان خنک میشود.
- هنگامی که قالب به طور کامل بسته می شود، قطعه به طور کامل شکل گرفته و پر شده است، که اساسا فاز پرشدن بعد از بسته شدن قالب را حذف می کند و بخش خنک کننده چرخه را کاهش می دهد.
مقایسه ی زمان چرخه ی روش تزریق معمولی و روش تزریق
**
برای اینکه که این فرایند با فشار پلاستیک کنترل شود، نه باسرعت، یک سنسور فشار نیز به سرنازل دستگاه اضافه می شود تا فشار واقعی پلاستیک را در لحظه ورود به راهگاه اندازه گیری نماید. این وسیله از فشار اندازه گیری شده به عنوان سیگنال اصلی کنترل در طول پر شدن قالب استفاده می کند. سنسورهایی نیز به قالب اضافه می شوند که نشانگر فشار در قالب و پیشانی جریان مذاب درون قالب می باشند.
بازخورد دریافتی از سنسورهای قالب برای ایجاد فشار مطلوب در قالب و ایجاد تغییرات لحظه ای در فشار تزریق بر اساس روند تغییرات درون قالب بسیار ضروری است. این سیستم همچنین توسط یک نمایشگر، به کاربر اجازه وارد نمودن پارامترهای فرآیند و نظارت بر آن را میدهد.
فرایند iMFLUX می تواند با اکثر انواع ماشین آلات تزریق پلاستیک، از جمله ماشین های تزریق هیدرولیک، تمام الکتریکی و هیبریدی، یکپارچه شود. بسیاری از کیت های نصب شده برای این تکنولوژی جدید از چندین تولید کننده بزرگ دستگاه های تزریق تامین می شود که با نصب بر روی دستگاه های خود، عملکردی سریع و ساده را ارائه می دهند. با این حال، iMFLUX را می توان با دستگاه های موجود هم هماهنگ کرد. این فرایند به طور موثری بر روی قالب هایی که به طور خاص برای iMFLUX طراحی شده اند و بر قالب های موجود در حال تولید کاربرد دارد.
این سیستم در صنایع مختلف از جمله خودرو، پزشکی، بسته بندی و تولید کالاهای مصرفی به کار برده می شود. کنترل فرآیند با یک مدار بسته و فشار کم و ثابت کنترل شده به این معنی است که اکثر پلیمرها با iMFLUX بهتر از محیط تزریق یک فرایند معمولی کار می کنند.
مزایای استفاده از فرایند iMFLUX از چهار تفاوت اصلی در مقابل روش تزریق معمولی برخاسته است:
- پر شدن قالب با فشار کم و ثابت.
فواید:
- نیاز به فشار قفل گیره پایین تر (استفاده از دستگاه با تناژ پایین تر)
- تنش پسماند کمتر در قطعه تولیدی
- کاهش پیچش در قطعه تولیدی
- دمای ذوب پایین
- زدگی کمتر در قطعه تولیدی
- تغییرات حفره به حفره کمتر در قالب های چند حفره ای
- ایجاد ضایعات کمتر مواد
- پر بودن قالب در هنگام بسته شدن.
فواید:
- چرخه سریعتر
- نشانه های فرو رفتگی کمتر
- خطوط جوش قوی تر
- بهبود سطح پایانی
- پر کردن با جریان یکنواخت و بدون وقفه.
فواید:
- خطوط جریان کاهش یافته
- بهبود جداره های نازک قطعه
- راه گاه سرد باریکتر
- استفاده از بازخورد فشار حفره در قالب.
فواید:
4.1. تولید قطعات ۱ تا ۳ درصد سبک تر
4.2.کاهش لکه در سطح قطعه
4.3. تنظیم اتوماتیک ویسکوزیته
4.4 اطلاع به موقع و موثر از حفره های مسدود شده
4.5 اطلاع سریع از وجود نشتی
4.6 تاثیر کمتر فرسودگی سیلندر در قطعه تولیدی
مقایسه میزان مصرف انرژی
- انرژی پر کردن در مقایسه با تزریق معمولی تا 50٪ کاهش می یابد زیرا iMFLUX از فشار پر کردن کمتری استفاده می کند و برای پر کردن قالب به انرژی برشی بالا متکی نیست.
- انرژی گیره تا 50% کاهش می یابد زیرا فشارهای پر شدن کمتر به تناژ گیره کمتری نیاز دارد.
- چرخههای سریعتر تلفات انرژی را در قسمتهای بیشتری پخش میکنند، در نتیجه مصرف انرژی را تا 20 درصد کاهش میدهد.
مواردی که iMFLUX جهت کار مطالعاتی استفاده شده و موفق بوده است:
مورد مطالعه اول :
تولید یک قطعه با جنس پلی کربنات با کاربرد در بخش پزشکی، به فرآیند iMFLUX تبدیل شد. مشتری به دلیل عدم توازن جریان در قالب ۱۶ حفره ای با راهگاه گرم ( هات رانر ) با ضایعات بالا و تولید قطعات ناقص مواجه می گردید.
iMFLUX میزان این ضایعات را از بیشتر از ۱۰٪ به کمتر از ۰.۲ % کاهش داد. این کار با بهبود بالانس جریان در هر کویته به دلیل پرشدن با فشار ثابت صورت پذیرفت. در این روش هر حفره فشار مشابهی را تجربه می کرد و هندسه نهایی قطعه در هر کویته گویای ثبات جریان می شد. همزمان با از بین بردن مشکل پر نشدن کامل قالب و به دست آوردن ۴۸٪ بهبود در توازن حفره، زمان چرخه نیز ۳۰٪ کاهش یافته است. در این مثال از دستگاه تزریق تمام الکتریکی برای استفاده از سیستم iMFLUX به صورت مدرن استفاده شده است.
مورد مطالعه دوم:
تولید قطعه ای از جنس PP که از جمله وسایل تمیزکاری منزل محسوب می شود. iMFLUX در مرحله طراحی قالب در سیستم تعبیه گردید. ضمن دانستن مزایای کاهش فشار، قالب برای به حداکثر رساندن قابلیت های این فن آوری طراحی شد. قالب و سیستم جدید iMFLUX اجازه استفاده از ماشین ۴۰۰ تن هیدرولیکی معمولی را می دهد، در حالی که تعداد کویته با ۵۰ درصد افزایش به ۱۲ حفره رسانده و چرخه را ۲۱ درصد کاهش می دهد. در مجموع، ۹۱ % بهبود عملکرد مشاهده می شود. حتی با افزودن چهار حفره و کاهش زمان چرخه، فشار تزریق پیک به طور کلی ۳۰٪ کمتر از فرآیند متعارف بود. در حالی که iMFLUX بر روی ماشینهای مجهز به ابزار لازم، موجود است، این مورد نشان می دهد که در طراحی قالب های جدید به خصوص برای فرآیند iMFLUX، مزایای قابل توجهی وجود دارد.
مورد مطالعه سوم:
تولید نوعی پریفورم PET در یک قالب چهار حفره بر روی یک دستگاه تزریق هیدرولیک با تکنولوژی iMFLUX اجرا شد. روند جدید با افزایش ۱۶ درصدی تولید در مقایسه با فرآیند متعارف به دست آمد. به طور متوسط، دستگاه ها با استفاده از قالبهای قدیمی خود نیز به ۱۵٪ تا ۲۵٪ بهبود عملکرد می رسند. با این حال، فرآیند iMFLUX همچنین عدم تعادل حفره را از ۶٪ به ۰.۸ ٪ کاهش داد، که این امر تنها با تقریبا نصف مقدار فشار مورد نیاز برای پر کردن قالب (از ۱۰۷۹ بار به ۶۲۲ بار )، و وزن متوسط را ۰.۴۸٪ کاهش داد، در حالی که تمام ابعاد و مشخصات فنی به همان صورت پابرجا بوده است. همانطور که قبلا توضیح داده شد، یکی از ویژگیهای روش iMFLUX پرشدن در حین بسته شدن قالب می باشد. این امر باعث کاهش فشار مورد نیاز می باشد، علاوه بر این، این امر باعث مصرف بهینه مواد در قطعه تولیدی شده و ضمن کاهش وزن قطعه نهایی باعث می گردد زمان چرخه ۱۳٪ کاهش یابد.
مورد مطالعه چهارم:
تولید یک قطعه از قطعات خودرو با مواد PP در یک دستگاه هیدرولیکی ۵۵۰ تن اجرا شد. قبلا این پروسه در یک سیکل ۵۰ ثانیه ای اجرا می شد، اما از استفاده از iMFLUX مدت زمان چرخه به ۸ ثانیه کاهش یافت که باعث افزایش بازده تولید تا ۲۰٪ گردید. همانطور که در مورد مطالعاتی سوم توضیح داده شد، بسته شدن و پر شدن همزمان قالب در تولید این قطعه باعث کاهش فشار به میزان ۱۴٪ و ۱٪ کاهش وزن شد. مهمتر از همه اینکه توانایی iMFLUX برای جذب و کاهش تغییر در ویسکوزیته مواد، میزان ضایعات را از ۱۸ درصد به ۲/۰ درصد کاهش داد.
دیدگاهتان را بنویسید